The Problem:
Inefficient Intercompany Processes
A cosmetics group managing both manufacturing and retail operations faced significant challenges due to inefficient intercompany processes. The issues included:
- Inaccurate Inventory Data: Discrepancies arose from delays in information sharing between the manufacturer and retailer, leading to inaccurate inventory levels and stockouts.
- Manual Data Entry: The reliance on manual handling of financial documents, such as invoices and bills, was time-consuming and prone to errors, resulting in data inconsistencies.
- Slow Financial Reconciliation: Processing and reconciling financial documents across entities was cumbersome, hindering financial visibility and timely decision-making.
- Limited Transparency: A lack of visibility into intercompany transactions made tracking progress and identifying potential issues difficult, ultimately affecting operational efficiency.
The Solution:
Automating Intercompany Processes with Odoo and BPMN
A cosmetics group managing both manufacturing and retail operations faced significant challenges due to inefficient intercompany processes. The issues included:
- Inaccurate Inventory Data: Discrepancies arose from delays in information sharing between the manufacturer and retailer, leading to inaccurate inventory levels and stockouts.
- Manual Data Entry: The reliance on manual handling of financial documents, such as invoices and bills, was time-consuming and prone to errors, resulting in data inconsistencies.
- Slow Financial Reconciliation: Processing and reconciling financial documents across entities was cumbersome, hindering financial visibility and timely decision-making.
- Limited Transparency: A lack of visibility into intercompany transactions made tracking progress and identifying potential issues difficult, ultimately affecting operational efficiency.
The Process
The implementation of the solution involved several structured steps:
- Gap Analysis: Conducted a comprehensive analysis to identify inefficiencies and areas for improvement in the existing intercompany processes.
- BPMN Workflow Design: Designed BPMN-based workflows to automate key intercompany processes, ensuring clarity and alignment between all parties.
- Odoo Configuration: Configured Odoo to automate the generation of sales orders, invoices, and bills, creating seamless connections between retail and manufacturing operations.
- Data Migration: Migrated existing data into Odoo, ensuring a smooth transition without data loss.
- Testing and Validation: Performed rigorous testing and validation of the new system to ensure it met all operational requirements and was ready for live use.
- Training and Support: Provided comprehensive training to the client’s team on using the new system and offered ongoing support to address any questions or issues.
BPMN Workflow Description
The BPMN file describes a simplified multi-company manufacturing workflow involving three main participants:
- External Retail Company Sales Process
- Supplier
- Internal Retail Company Purchase Process
The participants (shown as different pools) indicate that the flow involves collaboration between a retailer, a supplier, and an internal company managing the purchasing process.
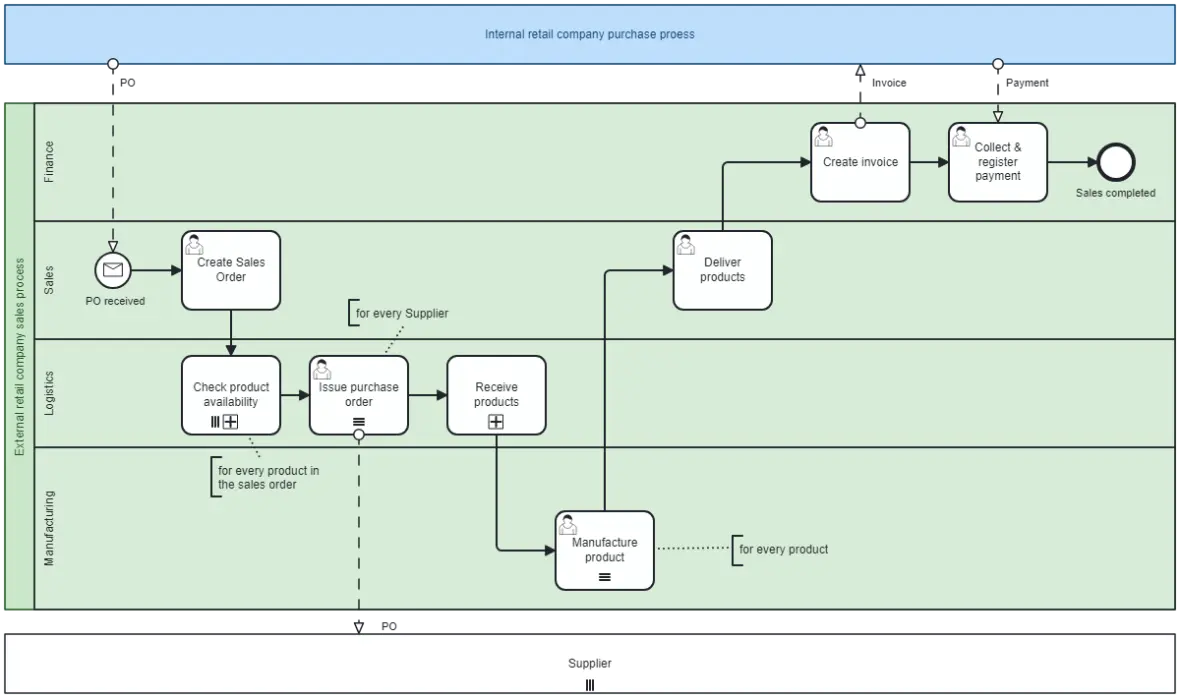
Story of the Workflow
The External Retail Company starts by managing its Sales Process, where customer orders are received and processed. As orders come in, the company checks its internal inventory and finds that products need to be procured. This triggers the interaction with the Internal Retail Company, which manages the Purchase Process.
The internal retail company reviews the order, checks its stock or availability, and if needed, reaches out to a Supplier to fulfill the demand. The supplier, upon receiving the Purchase Order from the internal company, prepares the requested products and delivers them as required.
Once the products are received, the internal company completes the transaction and supplies the necessary products to the external retail company, which can then fulfill its customer orders. The process continues smoothly, ensuring that each party plays its role to meet customer needs in a coordinated, multi-company manufacturing workflow.
Results: Improved Efficiency and Transparency
The implementation of the solution yielded significant outcomes, including:
- Reduced Manual Effort: The automation of intercompany processes eliminated the need for manual data entry and reconciliation, allowing staff to focus on higher-value tasks.
- Enhanced Data Accuracy: Real-time synchronization of inventory and financial data ensured accurate reporting, leading to improved decision-making.
- Increased Transparency: Enhanced visibility into intercompany transactions fostered better communication and collaboration between the manufacturer and retailer.
- Faster Financial Reconciliation: The streamlined processing of financial documents significantly reduced the time required for reconciliation, improving financial oversight.
- Optimized Inventory Management: Accurate inventory data and automated order processing led to better inventory management, minimizing stockouts and excess inventory.
By automating intercompany processes using Odoo and BPMN, the cosmetics group successfully transformed its operations, achieving greater efficiency, improved transparency, and enhanced financial performance. The streamlined workflows and real-time data synchronization enabled the group to respond quickly to market demands, improve collaboration, and make informed, data-driven decisions to drive growth.